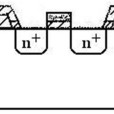
自对準工艺
用多晶硅版刻出多晶硅图形,再用有源区版刻掉有源区上的氧化层,高温下以n型杂质对有源区进行扩散(1000℃左右)。此时耐高温的多晶硅和下面的氧化层起掩蔽作用。
设计这类电晶体时往往让栅区宽度(栅氧化膜及其上的铝栅电极两者)比源和漏扩散区的间距要大一些,光刻时使栅区的两端分别落在源和漏扩散区上并有一定余量,由此便产生了较大的栅对源、漏的覆盖电容,使电路的开关速度降低。
基本介绍
- 中文名:自对準工艺
- 外文名:self-alignment technique
- 含义:实现光複印自动对準的技术
- 内容:详见正文
自对準技术
self-alignment technique
微电子技术中利用元件、器件结构特点实现光複印自动对準的技术。早期的 MOS积体电路採用的是铝栅工艺,首先在硅单晶片上热氧化生长一层二氧化硅膜,经第一次光刻,在二氧化硅膜上刻蚀出源和漏扩散视窗,用扩散法形成源和漏扩散区 (图1aMOS积体电路铝栅工艺),接着在硅片上形成新的二氧化硅层;再经过第二次光刻,刻蚀出栅区,生长栅氧化层;然后,经光刻刻出引线孔,完成蒸铝和刻铝等后工序;最后形成MOS电晶体。因为栅区必须在源和漏扩散区正中间,并需要稍覆盖源区和漏区,第二次光刻以及形成铝栅电极的那步光刻,都必须和第一次光刻的位置精确对準(图1bMOS积体电路铝栅工艺)。否则,栅区与源区或漏区就可能衔接不上,使沟道断开(图1cMOS积体电路铝栅工艺),致使MOS电晶体无法工作。因此,设计这类电晶体时往往让栅区宽度(栅氧化膜及其上的铝栅电极两者)比源和漏扩散区的间距要大一些,光刻时使栅区的两端分别落在源和漏扩散区上并有一定余量,由此便产生了较大的栅对源、漏的覆盖电容,使电路的开关速度降低。
随硅栅工艺的发展,已实现栅与源和漏的自对準。这种工艺是先在生长有栅氧化膜的硅单晶片上澱积一层多晶硅,然后在多晶硅上刻蚀出两个扩散视窗,杂质经视窗热扩散到硅单晶片内,形成源和漏扩散区(图2MOS硅栅工艺自对準示意图),同时形成导电的多晶硅栅电极,其位置自动与源和漏的位置对準。按照这种自对準工艺,栅与源和漏的覆盖由杂质侧向扩散完成,比铝栅工艺的覆盖电容要小很多。採用离子注入掺杂工艺的杂质侧向扩散更小,用它代替硅栅工艺中的热扩散工艺,能进一步减小栅对源和漏的覆盖电容。此外,在铝栅工艺中,即使铝栅电极比沟道短,也可增加一步离子注入工艺填充栅区旁的未衔接部分,实现自对準(图3MOS铝栅工艺实现自对準的示意图),藉以减小寄生电容,可提高MOS积体电路的开关速度和工作频率,同时也减小器件尺寸而提高电路的集成度。
在双极型电晶体及其积体电路的製造中,也多採用自对準工艺。例如,用微米级线宽的多晶硅发射极作掩模,再扩散杂质形成浓基区,以实现发射极与基区的自对準。又如超自对準工艺的主要工序是用通常方法完成基区掺杂后,在硅片上澱积一层未掺杂多晶硅,氧化掉不必要的部分。在整个晶片上澱积氮化硅膜层和二氧化硅膜层。除发射区和集电极接触孔外,其他部位的二氧化硅膜全腐蚀掉。以二氧化硅膜作掩模,把硼注入到未掺杂多晶硅内,然后腐蚀掉氮化硅(稍微过腐蚀一点)。再採用选择腐蚀法把未掺杂多晶硅腐蚀去,暴露的基区宽度小于1微米。採用热氧化,同时形成P□区。去掉氮化硅,不用掩模进行硼注入,自对準形成P□基区。再在多晶硅发射极中掺入砷,扩散形成发射区。其他后续工序与通常的双极型积体电路工艺相同。用这种方法製成的双极型电晶体,实现了多晶硅发射极与P+基区的自对準,有较小的基区电阻和较小的发射极-基极结电容,多晶硅发射极和多晶硅基极间距小于1微米,提高了双极型积体电路的速度,也提高了电路的集成度。用这种技术已製成存取时间为2.7纳秒发射极耦合逻辑电路的1千位随机存储器。